The manufacturers of the world’s first 3D-printed horse trailers, which could be on the market next year, say they hope to combat supply, cost and labour issues, while producing vehicles more quickly and accurately.
Double D Trailers, based in North Carolina, US, announced last week it was launching the new product, to a huge response.
“Some people were saying ‘This is fantastic’, others that we’re idiots!” owner Brad Heath told H&H. “But it’s been overwhelmingly positive, and we’re really excited to see where this leads us.”
Mr Heath explained that since a car was fully 3D printed in 2014, the technology has moved forward in leaps and bounds; the aerospace and automotive industries using it in particular.
Some five years ago, he saw Ingersol Machine, a company in Illinois, had made a 3D printed boat.
“It was impressive,” he said. “I reached out to them and they had the largest 3D printer in the world; I think the cost of the equipment was about $3m. The costs were astronomical.”
Since then, knowledge of the best combinations of materials for strength and precision has advanced, Mr Heath said, but also since then, the effects of Covid have made themselves felt.
“The pandemic hit our manufacturing so we’re still 10 months out,” he said. “If you want a new trailer, I can sit and talk to you but I can’t do it for 10 months. Then there are supply chain issues, and inflation – our costs have increased 54% so a trailer than was $100,000 is now $154,000. Plus our unemployment rate is the lowest it’s been for 50 years and business can’t hire people. So when I revisited this about a year ago, I found it solves a lot of the issues we’re facing.”
Mr Heath explained that all the components such as latches, doors and bolts can be printed in house, instead of potentially waiting for weeks for a part to be delivered.
“We’ll print the ‘glass’ from a translucent material that will be strong enough not to break if you hit it with a hammer,” he said. “It’s pretty impressive stuff.”
Double D Trailers has been working with reputed design company One One Labs in Poland, and engineering firm Loci Robotics. Once the designs for the trailer and components have been finalised, these are added to a computer system, and the designs sent to the 3D printers. Pellets of the material used are fed into the printers and melted down, then the part hardens immediately it comes into contact with the air.
“When I first talked to [the companies] they said did I want to weld together a steel chassis and print a box to go on top and I said ‘Heck, no!’” Mr Heath said. “We’ll set up small machines to print the components, and we can print as much detail as we want, down to about 1/32 of an inch, but the main structure will be one print, with no seams, no joints. Then we’ll roll it into another bay, and add the doors, windows and other components.”
These include tyres, wheels and axles, about the only parts Mr Heath said would have to be bought in, which means a smaller carbon footprint but also less margin for error as there are fewer parts to be installed by hand.
Areas of the build that need to be stronger, such as the floor, will be printed at greater thickness. The floor and chassis will be carbon fibre – “one of the strongest, lightest materials available” – and the rest polycarbonate and fibreglass fill.
The plan is to have a small, desktop prototype finished this month, and a full-size prototype this summer, which will be subject to “a tremendous amount of testing”.
“We’ll do our damndest to see what we can break and mess up!” Mr Heath said. “As well as seeing what temperatures it can stand. When we’ve finished, and can back up all our claims, at that point, we’ll be ready to roll up our sleeves and say ‘You want one of these? We’re ready’.”
Mr Heath hopes the first trailers will be on sale in 2024, at a higher price compared to their traditional equivalents; more like $70,000 than $50,000-55,000, but this will depend on the final cost of the exact materials used.
Should a component break, the customer can order a new one to be printed from its specific design, and Mr Heath said in theory, it should be possible to melt down a whole trailer and reprint it.
“Maybe we’ll have a 10-year warranty; if it’s totalled in an accident, for example, we’ll just grind it up and print it again,” he said. “We’ll still be making the traditional ones too; it takes a long time for people’s mentality to change, but we’re excited about where this goes.”
You might also be interested in:
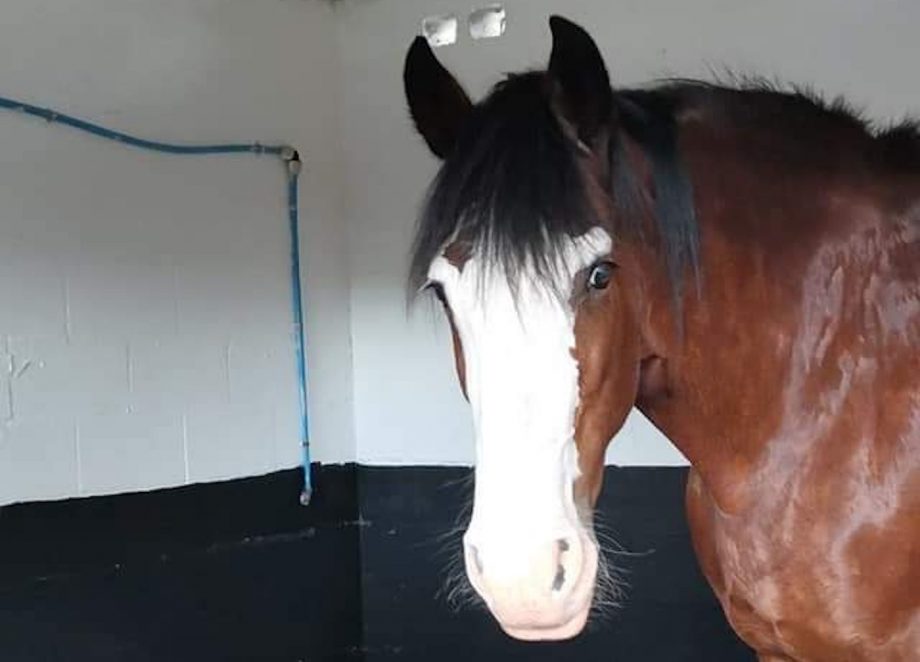
Clydesdale’s canker cured thanks to top farriery – and 3D printed plates
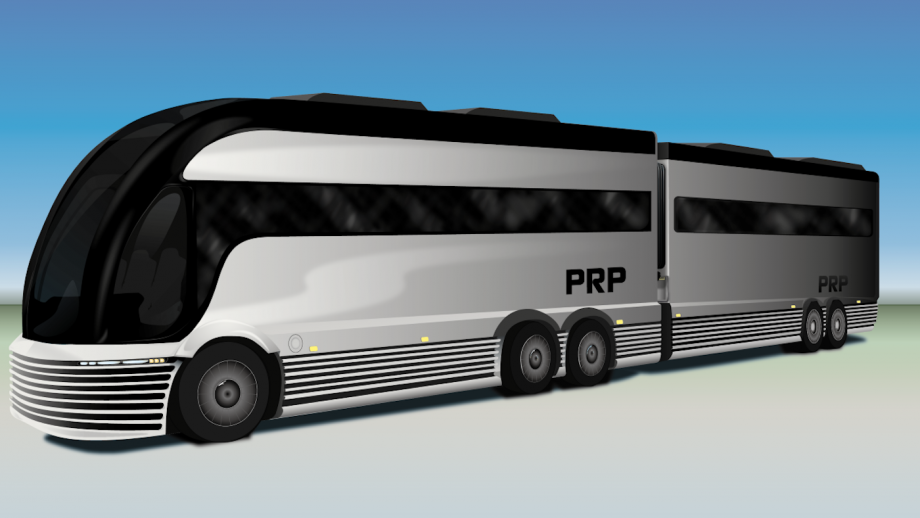
Is this the emission-free, diesel-free horsebox of the future?
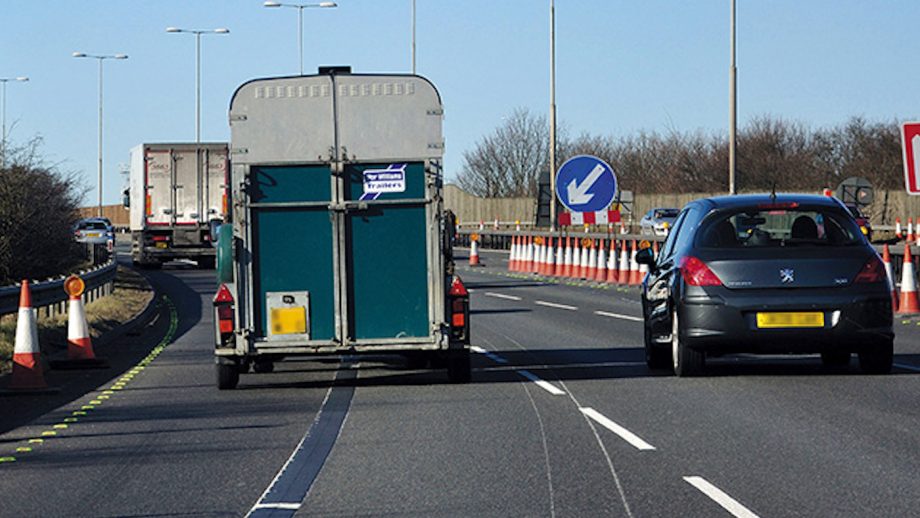
Baler twine tied to outside of horseboxes – DVSA clarifies the rules
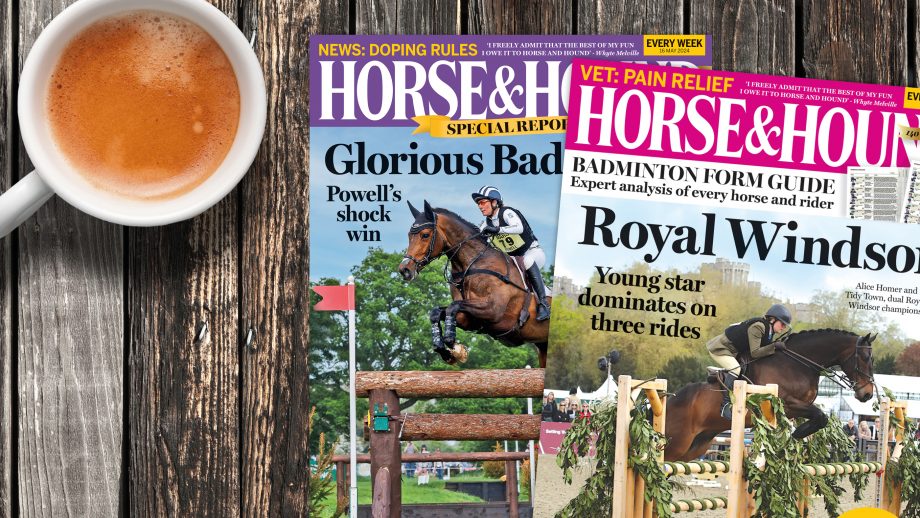
Subscribe to Horse & Hound magazine today – and enjoy unlimited website access all year round
Horse & Hound magazine, out every Thursday, is packed with all the latest news and reports, as well as interviews, specials, nostalgia, vet and training advice. Find how you can enjoy the magazine delivered to your door every week, plus options to upgrade your subscription to access our online service that brings you breaking news and reports as well as other benefits.